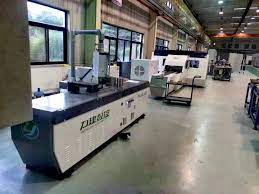
In the dynamic landscape of modern industries, busbar machine technological advancements have continually reshaped the way we approach manufacturing processes. One such innovation that stands out is the bending machine, a versatile and indispensable tool that has revolutionized the fabrication of various materials. Bending machines, often referred to as press brakes, have become a cornerstone in industries ranging from automotive and aerospace to construction and consumer goods.
At its core, a bending machine is designed to shape and transform flat sheets of metal or other materials into intricate three-dimensional forms. This remarkable capability stems from the machine’s ability to exert force at specific points, allowing for precise bends, angles, and curves. This versatility has opened the door to a multitude of design possibilities that were previously constrained by manual methods or limited machinery.quality control by detecting anomalies or deviations during the bending process.
The evolution of bending machines has been characterized by a shift from traditional hydraulic systems to more advanced computer numerical control (CNC) technology. This transition has brought about unprecedented levels of accuracy, repeatability, and automation. Modern CNC bending machines can be programmed to execute complex sequences of bends with minimal human intervention, resulting in reduced production times and increased productivity.
Industries that require customized components or large-scale production batches have particularly benefited from bending machines. The automotive sector relies on these machines to shape intricate parts with precision, ensuring optimal fit and function. In architecture and construction, bending machines play a pivotal role in crafting structural elements like beams, pillars, and façades that demand both aesthetic appeal and structural integrity.Moreover, their real-time monitoring capabilities enhance .